On 20th December 2023, we conducted a TOYOTA factory tour in Ban Pho as part of employee education training. This was a great opportunity to see the main manufacturing factory of TOYOTA, which has been a leading Japanese company in the world.
Greetings, Introduction Videos of TOYOTA, Explanations and Cautionary Notes on Factory Tour
Before the factory tour started, we got greeted from the factory supervisor and then watched a introduction video of TOYOTA business and initiatives in Thailand.
We learned about the company’s corporate philosophy, overview of the three factories in Thailand, TOYOTA’s outstanding technological capabilities, and efforts to create sustainable value. We were very surprised to know that the Ban Pho Factory has a site area of 2,560,000 square meters, that it takes only 55 seconds to assemble one car at the assembly factory, and that it uses a unique production system called *TPS.
Next, we had a lecture for the factory tour, and we were given red hats so they could be distinguished as visitors inside the factory, and transceivers to listen to the explanations during the tour. Later on, we took the hat back home, which was a memorable item for our factory tour.
*TPS stands for TOYOTA Production System, which has been made to completely eliminate seven wastes on the production line (overproduction, waiting time, transportation, processing, inventory, operation, and defective products). This idea is about to keep as little inventory as possible, and instead supply what we need, when we need it, and in the amount we need.
Assembly Factory Tour
We drove to the assembly factory and we were guided to catwalk-like area where we could see the inside of the factory from above. We witnessed how a car is assembled step by step through the collaboration of humans and robots, and was overwhelmed by the grand scale. There was a machine that used sensors and lights to notify people when handling different types of parts to prevent them from making mistakes, and we got a glimpse of the coexistence of humans and machines. Inside the factory, there is a mechanism called Karakuri Area, which uses the force of gravity to move parts without using electricity or human power, making it sustainable. We were impressed with that area incorporating Japanese characteristics as well. There were also thorough efforts to improve product quality, such as the inspection dojo (product inspection) and the skill refreshment area (updating technology and knowledge), which was truly amazing.
Question-and-Answer Session
At the end of the tour, a question and answer session was held, and many of us actively asked a variety of questions. We learned that TOYOTA values the happiness and work comfort of its employees, because TOYOTA has the high proportion of Thai employees and Thai executives, generous welfare benefits, and bonuses given to contract employees, which impressed us very much.
Summary
All the employees who participated in the tour gained motivation for their future work and learning through this valuable experience. It was also a great opportunity to understand the car industry as we work with customers in the manufacturing industry.
We regularly conduct factory tours like this to educate our staff.
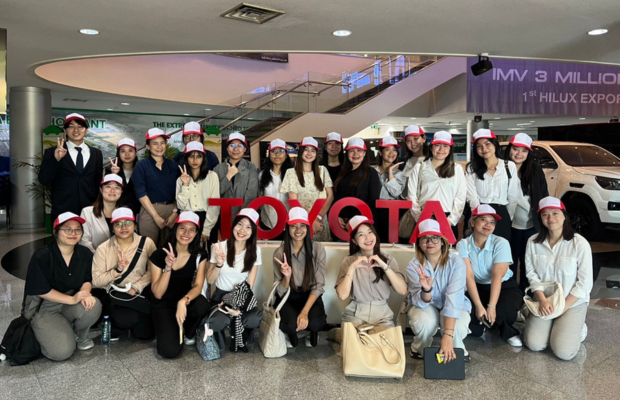
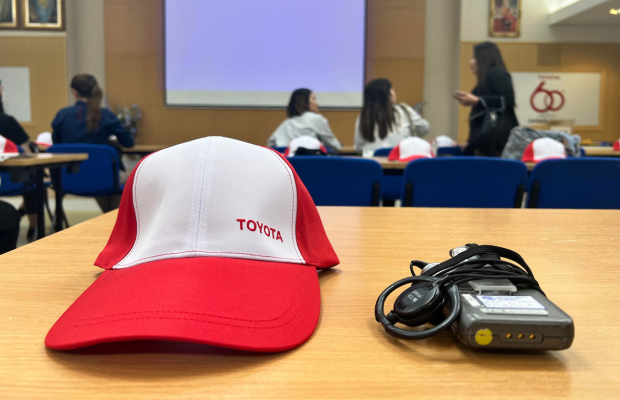